Revolutionizing Medical Device Manufacturing With 3D Printed Injection Molds
Innovation continues to reshape traditional processes in medical device manufacturing, and one such groundbreaking advancement is the integration of 3D printing technology for creating injection molds. Historically reliant on conventional machining techniques involving steel or aluminum tooling, the landscape has rapidly evolved with the advent of liquid resin printing. This transformation has empowered medical device manufacturers to revolutionize their production timelines, enabling the swift creation of intricate molds in a matter of hours, a feat previously unattainable within the industry.
Traditional methods involving steel or aluminum injection mold tooling have long been the stalwarts of medical device production. However, these methods are often marred by prolonged lead times, intricate design limitations, and considerable costs associated with outsourced tooling. The transition to liquid resin-based 3D printing has ushered in a new era, offering an array of advantages that have significantly reshaped the manufacturing process for medical devices. This blog will examine these advantages as well as explore some of the challenges and limitations that have been overcome to achieve this revolutionary creation.
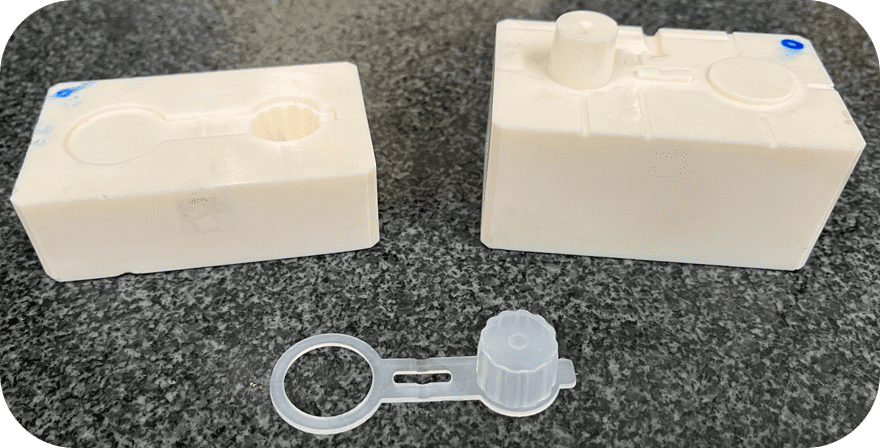
Top 3 Advantages of Shifting to Liquid Resin-based 3D Printing
- Speed and Agility – The key catalyst behind this paradigm shift is the speed and agility afforded by liquid resin printing technology. Unlike the protracted waiting periods of weeks associated with outsourced traditional tooling, 3D printing injection molds now allow for on-site, rapid fabrication in a matter of hours. This remarkable reduction in production time not only accelerates the overall manufacturing process but also enhances the agility of responding to design iterations and market demands.
- Flexibility and Precision – The flexibility and precision offered by 3D printing technology contribute significantly to its appeal in medical device manufacturing. The intricate geometries and complex designs required for various medical devices, such as intricate surgical instruments or patient-specific components, were once challenging or economically unfeasible with traditional methods. Liquid resin 3D printing circumvents these limitations, enabling the fabrication of highly intricate molds with unparalleled precision, thereby facilitating the production of complex medical devices that meet stringent quality standards.
- Cost effective – The cost-effectiveness of in-house 3D printing for injection molds is a game-changer for medical device manufacturers. The ability to rapidly prototype and iterate designs in-house significantly reduces expenditure associated with outsourcing tooling, while simultaneously streamlining the overall production process. This cost-efficient approach not only saves valuable financial resources but also enhances the competitiveness of manufacturers in the dynamic healthcare market.
This mold was printed on the Axtra3D Lumia X1 out of the Hi-Temp AMB 300 resin from 3D Systems. This material has a heat deflection temperature of 300 C. That means the part will not warp or change shape under 300 C.
Challenges and Limitations Exist But Can Be Overcome
While the advantages of 3D printing injection molds for medical devices are undeniable, challenges and limitations persist. Material selection, ensuring biocompatibility, and durability are crucial factors that demand meticulous attention. Manufacturers must rigorously assess and validate materials to ensure compliance with regulatory standards, guaranteeing the safety and efficacy of the final medical devices.
Some of the limitations that have been overcome to achieve this are:
- Speed or printing – Hybrid Photosynthisis (HPS) printing technology from the Axtra3D Lumia X1, SLA, and DLP allow you to print midsized molds in just a few hours, depending on the geometry.
- Heat Deflection Temperature improvements – Liquid resin materials have come a long way over the past few years with heat deflection temperatures of 300 C
- Hi Accuracy and Detail – Between the Axtra3D and 3D Systems, we have several options that can get you accuracy of +-0.002” across the entire build platform. This allows you to get extreme detail and print very small features within your mold cavity.
- Less material waste – 3D printing is an additive manufacturing method instead of subtractive machining. Machining creates waste because the metal block needs to be milled and then shaved into shape.
The evolution of liquid resin-based 3D printing technology has propelled the medical device manufacturing industry into a new era of efficiency, agility, and innovation. The ability to swiftly create intricate molds in-house, coupled with enhanced precision and cost-effectiveness, has redefined the production landscape. While challenges exist, the immense potential of 3D printing injection molds for medical devices is undeniable, promising a future where rapid, customized, and high-quality medical devices cater to the evolving needs of healthcare globally.
Nota3D is made up of 3D printing enthusiasts representing over 40 years of combined industry experience. With backgrounds in technical support, operations, applications, customer support & sales, we provide an all-in-one solution to the companies we serve.
What you can expect from us is a very personal approach coming from a place of genuine interest and curiosity. We feel it’s not right to recommend a solution until we have a full understanding of your processes (current & future). At that point, we will recommend a solution…even if that solution isn’t from us.
We want to be known as a trusted partner and that is our focus. That’s why several of the nation’s top companies come to us to find the right tools for the job. We’ve worked with everyone from garage inventors to the largest medical device companies in the world and the list keeps growing.
To find out more about how we can help contact us today.